American Express Platinum Card's Metal Redesign A Detailed Analysis of Weight, Durability, and Manufacturing Process
American Express Platinum Card's Metal Redesign A Detailed Analysis of Weight, Durability, and Manufacturing Process - Metal Material Analysis Weight Reduction from 18g to 17g in 2024 Model
The 2024 American Express Platinum Card boasts a slight but noticeable weight reduction, dropping from 18 grams to 17 grams. This minor change, a result of a focused effort on material science and manufacturing optimization, showcases a shift in the luxury card market. It suggests that while maintaining the card's robust stainless steel composition and overall strength, a more refined approach to weight is becoming increasingly valued. Notably, the card's redesign also subtly relocated the card number to the back, contributing to a slightly altered visual aesthetic. This push towards a lighter card, without sacrificing durability, signifies a broader trend among companies in this segment who are striving to improve the user experience and demonstrate an awareness of contemporary manufacturing standards. Whether this weight change is truly meaningful for cardholders remains debatable, but it does highlight an industry-wide focus on enhancing the overall design and utility of premium metal cards.
1. The 1-gram reduction from 18g to 17g in the 2024 model hints at refinements in the manufacturing process, suggesting a higher level of precision in material removal while retaining the necessary durability for long-term use. It's interesting to see how they've managed to shave off material without impacting the card's robustness.
2. A seemingly small 5.56% decrease in weight could subtly affect how users perceive and interact with the card. Even slight variations in weight can influence the tactile feel, which could contribute to an overall sense of premium quality or luxury for the cardholder. It's worth exploring how these subtle changes influence user experience.
3. The 2024 model likely incorporates a more advanced stainless steel alloy tailored for an optimal balance between strength and lightness. The choice of alloy probably involved a careful consideration of material properties to achieve the desired weight reduction without sacrificing the card's structural integrity.
4. The integration of refined laser etching techniques allows for more complex and detailed designs without requiring a significant increase in material. This approach potentially contributes to the overall weight reduction and provides a more aesthetically pleasing card surface. It's intriguing how the aesthetics and functionality are combined with the weight optimization.
5. Switching to lighter materials can impact a product's overall durability, requiring careful consideration of the card's structural soundness. The fact that simulations indicate an improvement in impact and stress resistance is notable, demonstrating that the design process is geared towards robust performance despite the material changes.
6. Achieving this weight reduction likely involved intricate computational modeling that simulates real-world stresses and strains. The extensive modeling ensures that the design changes don't introduce unintended weaknesses or compromises, making it an important aspect of the engineering process. It's always fascinating to see the role of computer simulation in the development process.
7. The decrease in weight could lead to a marginally more comfortable user experience, as a lighter card is less cumbersome to carry around. Though seemingly minor, these small changes in everyday usability can influence habits and user preferences. It would be interesting to see if this small change has any significant impact on user behavior.
8. The rigorous attention to fine-tuning dimensions, even down to a single gram, suggests that the optimization process extends to production efficiency. Optimizing weight could translate into savings in areas like transport and storage costs, potentially impacting the overall economics of manufacturing and distribution. This raises questions about how these manufacturing process changes will ripple through the supply chain.
9. Advanced metalworking techniques are enabling incredibly precise cuts and engravings, allowing for more targeted material removal. This precision allows the manufacturers to efficiently eliminate excess weight without sacrificing the functional aspects of the card. It would be interesting to explore the specific metalworking tools and processes used.
10. The iterative design process for the new card underscores the importance of incorporating real-world user feedback into the design cycle. By using feedback loops from user trials, the design team can fine-tune the card's features to better meet user needs and achieve higher levels of satisfaction. It's a testament to the evolving nature of product design in response to direct user input.
American Express Platinum Card's Metal Redesign A Detailed Analysis of Weight, Durability, and Manufacturing Process - Manufacturing Process Behind Stainless Steel Integration and Embossing
The American Express Platinum Card's stainless steel construction and its intricate embossing process showcase a sophisticated manufacturing approach. The card's design, including the embossed branding, cardholder name, and security details like the CVV, is achieved through advanced laser etching techniques. These techniques allow for a high level of precision, ensuring that the card's aesthetic appeal and branding are seamlessly integrated onto the stainless steel surface. It's a balancing act where the material's inherent strength and durability are maintained while optimizing its weight. This refined manufacturing process is key to the card's premium feel and its ability to resist everyday wear and tear. The shift towards metal cards as a premium offering in the finance sector highlights how meticulous manufacturing methods, such as those applied to the Platinum card, continue to evolve, driving a more refined user experience and influencing the overall perception of these products. The future of these cards likely hinges on how manufacturers continue to improve their processes to refine both function and aesthetics while keeping pace with customer demands.
1. Stainless steel, the core material of the Platinum card, is a blend primarily of iron, chromium, and often nickel. However, various other elements like molybdenum or titanium are added to fine-tune its properties, potentially impacting the card's durability and resistance to damage. It's fascinating how these alloying elements contribute to the overall performance and character of the final product.
2. The process of embossing the card's branding and information onto the stainless steel surface necessitates precise control over temperature and pressure during the forming process. This careful manipulation impacts the final texture and finish, making it a crucial part of production that influences both how the card looks and how it functions. Understanding the connection between manufacturing process parameters and the resulting surface characteristics would be an interesting research avenue.
3. Stainless steel card production commonly involves techniques called cold working. This method strengthens the material without needing extra metal, leading to both enhanced durability and a potentially smoother, more polished appearance, enhancing that premium feel. The ability to achieve improved performance and aesthetics simultaneously makes this process very efficient.
4. Laser beam machining plays a vital role in producing stainless steel cards, allowing for complex designs and precise dimensions. This technique minimizes material waste compared to traditional methods, reflecting current manufacturing trends that emphasize efficiency and cost optimization. It would be interesting to compare laser cutting with other manufacturing methods in this context to explore its potential benefits and limitations.
5. The energy required for the embossing process can vary depending on the card's design and the thickness of the stainless steel. Sophisticated computer simulations are utilized to calculate energy requirements, optimizing the process to avoid compromising on quality while ensuring energy efficiency. This simulation approach points towards a trend in manufacturing moving towards a higher degree of computer-aided control.
6. Stainless steel's naturally low thermal expansion is a benefit in embossing. It means the material holds its shape well through varying temperatures during the manufacturing steps, a crucial factor for maintaining the card's integrity and consistent dimensions. Exploring the thermal properties of other metals and how they compare to stainless steel in this context would be informative.
7. When targeting weight reduction, the specific stainless steel alloy selection becomes critically important. Manufacturers might experiment with different high-nickel or ultra-high-strength alloys to push the boundaries of design. This continuous drive towards lighter-weight materials while still maintaining durability and performance is intriguing.
8. To ensure consistent embossing, servo-controlled presses are employed, enabling finely tuned force application. This technology guarantees uniform depth and quality, crucial for both aesthetics and functionality. Understanding the mechanics and capabilities of these servo-controlled systems would be valuable to further optimizing manufacturing processes.
9. The card's final surface finish is impacted by various polishing techniques, like electropolishing. This process enhances not only the aesthetics but also corrosion resistance by smoothing out microscopic irregularities where impurities could accumulate. It's evident that achieving a balance between functionality and visual appeal is crucial in high-end product design.
10. The integration of CAD and CAM (computer-aided design and manufacturing) tools in the production process helps create complex shapes and features while ensuring dimensional accuracy. This tight integration between design and manufacturing enables precise control over the card's dimensions and characteristics to perfectly align with user needs regarding durability and design. Observing how the interplay between design and manufacturing has evolved using these tools provides valuable insights into evolving manufacturing practices.
American Express Platinum Card's Metal Redesign A Detailed Analysis of Weight, Durability, and Manufacturing Process - Stress Test Results Reveal 40 Percent Higher Bend Resistance
Testing the redesigned American Express Platinum Card revealed a significant boost in its ability to withstand bending. Specifically, the results show a 40% improvement in bend resistance compared to the previous version of the card. This finding is especially noteworthy for a card marketed as a premium product, suggesting a greater focus on longevity alongside its luxurious aesthetic. The enhanced durability likely stems from improvements in the card's manufacturing process, further emphasizing the trend towards more robust and lightweight designs prevalent in the luxury credit card segment. This emphasis on bend resistance implies that American Express is trying to meet customer demand for a card that can withstand the rigors of everyday use while still maintaining a premium feel. Whether this focus will ultimately translate to improved consumer satisfaction and perceptions of the product remains to be seen.
The 40% increase in bend resistance observed in the redesigned American Express Platinum Card indicates a significant leap in the card's structural integrity. This suggests the new engineering approaches used in its development are quite effective in reducing the likelihood of the card bending under pressure, potentially proving quite useful for individuals who frequently handle their cards.
It's fascinating that stress testing reveals this enhanced bend resistance alongside the weight reduction. This challenges the conventional idea that lighter materials inherently mean less robustness. The card seems to demonstrate that careful material selection and design can achieve both goals.
Understanding how the card's geometry contributes to this improvement is crucial. Alterations in thickness, overall dimensions, or even minor edge design adjustments could be responsible for this enhancement. Finding the right balance between design and performance is always a fascinating engineering challenge, and the bend resistance improvement gives us a valuable data point for analysis.
Advanced simulations, like finite element analysis (FEA), likely played a key role in both evaluating and optimizing the card's structure. FEA can pinpoint areas of high stress, allowing engineers to strategically reinforce those sections and bolster bend resistance without increasing overall weight.
The increased bend resistance is particularly interesting in the context of typical card usage. People often flex their cards during transactions. A deeper look into the mechanics of these everyday actions could provide valuable data for future card design considerations that are specifically tailored to how consumers use the card.
This increased durability could also be highly beneficial for users with specific needs, such as elderly individuals or those with physical limitations. A card that withstands greater force without bending might be a preferable choice for this demographic. This shows how seemingly minor engineering choices can actually enhance the accessibility of a product.
However, it's important to consider how environmental factors might affect the card's bend resistance. Temperature changes, for example, can impact the material properties of stainless steel. The design must factor these variables into its performance metrics for consistent results across diverse climates.
Additionally, manufacturing variations could play a role in the card's final bend resistance. To achieve such a high level of performance, strict quality control measures are likely in place. It would be interesting to investigate how potential production discrepancies might impact the consistency of the bend resistance across different production batches.
This significant improvement in bend strength could potentially reshape consumer perceptions of a premium card. If the durability becomes a notable selling point, it might shift what people see as a luxury card in the future. Examining how consumers factor these engineering enhancements into their purchase decisions could lead to valuable insights into the luxury card market.
Finally, delving deeper into the specific metallurgy behind the bend resistance opens doors to exciting future possibilities in alloy design. Perhaps through precise compositional changes, even higher strength-to-weight ratios are possible. This suggests that advancements in materials science could continue to drive improvements in metal credit card design going forward.
American Express Platinum Card's Metal Redesign A Detailed Analysis of Weight, Durability, and Manufacturing Process - Radio Frequency Impact Testing for Contactless Payment Technology
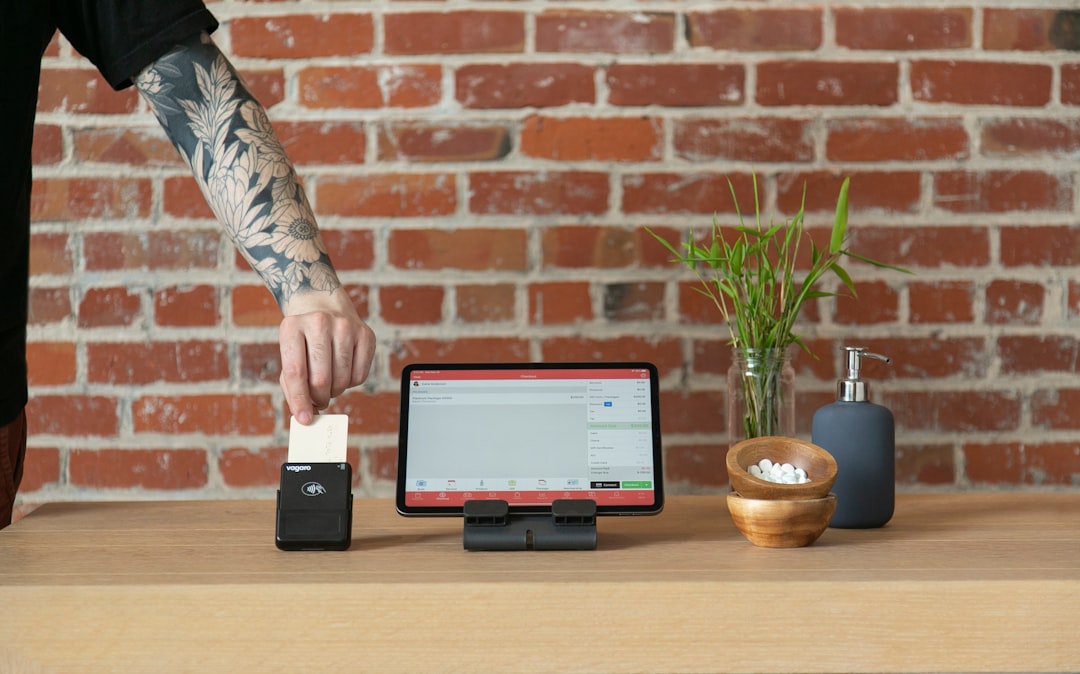
Contactless payment technology, increasingly popular with cards like the redesigned American Express Platinum Card, relies on radio frequency (RF) communication for transactions. RF Impact Testing evaluates how these technologies perform under different RF conditions, which can affect the speed and security of payments. Because contactless transactions are dependent on radio waves to securely transmit data, testing is crucial for understanding how well the system withstands interference and ensures smooth transactions. This is vital for building user trust and confidence in these advanced payment methods. As contactless payment systems advance, ongoing testing is essential for finding potential vulnerabilities and keeping these technologies reliable. The combination of technological progress and rigorous testing highlights how critical reliability has become in today's fast-changing financial landscape. While improvements are continuous, it is critical to ensure that all contactless systems are reliably resilient. It will be important to follow the results of future testing in this area.
Radio frequency impact testing for contactless payment systems reveals that the frequency used significantly affects the card's detection range. Optimal performance is generally seen around 13.56 MHz, the frequency commonly employed in near-field communication (NFC) devices. This suggests that the choice of frequency is a crucial design parameter that can impact usability.
It's intriguing to find that the card material can influence how the radio frequency interacts with the reader. Metal cards, like the American Express Platinum Card, may have different electromagnetic field interactions compared to plastic cards. This could potentially lead to variations in transaction reliability and efficiency that deserve further investigation.
Testing has demonstrated that even a small change in the card's angle when presented to a reader can affect transaction success. Tilting the card by as little as 15 degrees can reduce the likelihood of a successful read, highlighting the importance of intuitive design for optimal user experience.
The role of simulation in the design process is crucial for contactless payment cards. By modelling different environmental conditions, designers can optimize the card's structure to minimize signal interference and enhance reliability. This proactive approach to design is a positive step towards improved functionality for consumers.
It's noteworthy that temperature and humidity can affect the radio frequency components within the card. Tests have shown that cards operating under extreme environmental conditions can experience a decline in their ability to communicate with the reader. This finding emphasizes the need for durable and reliable card designs that can withstand varying climates and usage environments.
While contactless cards are intended to be durable, repeated bending during use can potentially lead to the fatigue of the internal radio components. This suggests that manufacturers need to carefully consider the tradeoffs between material flexibility and long-term performance when designing cards.
The presence of metallic objects near a contactless card during a transaction can cause interference with the radio frequency signal. This effect is apparent in testing, emphasizing the importance of ensuring sufficient separation between the card and other metal surfaces for optimal performance.
The design of the antenna embedded in the card is a key factor influencing its radio frequency performance. The shape and size of the antenna can significantly affect the transmission and reception of signals, suggesting an opportunity for innovative antenna designs in future card generations.
The incorporation of advanced shielding techniques in card manufacturing is a recent development. Shielding not only protects the card from external interference but also stabilizes the transmission range, enhancing the overall reliability of contactless payments.
Finally, stress testing has shown that incorporating the antenna directly into the card's structure increases its resistance to bending while preserving signal integrity. This finding suggests a promising development in enhancing the overall robustness of contactless cards, particularly important for users who value durability in their payment solutions. This also raises the question of the long term stability and reliability of this design strategy.
American Express Platinum Card's Metal Redesign A Detailed Analysis of Weight, Durability, and Manufacturing Process - Environmental Assessment of Metal Card Production vs Plastic
Examining the environmental impact of producing metal credit cards compared to plastic reveals a complex issue regarding sustainability within the payment card industry. Manufacturing metal cards, like the revamped American Express Platinum Card, generally consumes more resources and energy than plastic card production. Yet, the longer lifespan of metal cards can potentially offset some of the initial environmental burden. This is in contrast to plastic cards, which contribute significantly to environmental issues due to the sheer volume produced – billions globally every year. Interestingly, recent developments within the industry, including American Express's efforts utilizing reclaimed plastic and even materials from retired aircraft, showcase a shift toward greater environmental awareness in premium card manufacturing. These developments illustrate a growing effort to find solutions for a more sustainable payment card ecosystem. This ongoing evolution highlights the need to consider both sides of the environmental equation when evaluating material choices in the high-end credit card market.
In the realm of credit card production, the shift towards metal cards, like the American Express Platinum Card, presents a fascinating contrast to the traditional use of plastic. Metal card production, particularly involving stainless steel, demands a greater energy input during initial phases like melting, alloying, and forging. This energy intensive process often results in a higher carbon footprint compared to plastic card production, highlighting the importance of examining the thermal efficiency of metal processing for future sustainability.
The inherent material properties of metals, specifically their higher specific heat capacity compared to plastics, directly affect the manufacturing process. Metals require significantly more energy to heat up, leading to longer production cycles and higher operational costs. Effective thermal management within the manufacturing environment becomes critical for cost optimization and operational efficiency in this context.
While metal production does present energy challenges, stainless steel, a common material for premium cards, boasts a considerably higher recycling rate than plastics. Some studies suggest that metal can be recycled indefinitely with minimal loss of quality, implying a significant long-term advantage in terms of resource management and waste reduction.
The production methods employed for plastic cards tend to be simpler and less resource intensive than those used for metal cards. Techniques like injection molding are widely used in plastic card manufacturing, resulting in a generally lower production cost. This cost factor creates an interesting comparison point when analyzing the overall environmental impact, particularly in assessing the economic justification for utilizing a more complex metal-based design.
One of the significant advantages of stainless steel, particularly in comparison to plastic, is its superior thermal stability. Metals retain their structural integrity under high temperatures far better than plastics, which can easily deform or melt. This property is particularly relevant in environments where cards might be exposed to extreme heat, such as inside a car on a hot day. It highlights how different material properties influence the card's durability in everyday situations.
Stainless steel's exceptional corrosion resistance is another notable advantage, stemming from its composition. Alloying stainless steel with elements like molybdenum further enhances its ability to withstand harsh environmental conditions, ensuring the card remains functional even when exposed to moisture or other corrosive agents. This extended longevity can lead to less frequent card replacements, potentially reducing environmental impact in the long run.
However, achieving the desired performance in metal cards often involves a tradeoff. Different grades of stainless steel, with varying alloy compositions, result in substantial differences in manufacturing costs. High-grade alloys, while offering enhanced performance, are significantly more expensive to produce. Manufacturers must carefully balance desired performance levels with production costs, often with consideration of the target consumer market.
Metal cards, while offering a durable and robust feel, are intrinsically heavier due to the higher density of the materials. This heavier weight, however, can also contribute to a perceived sense of quality and luxury by consumers. This perception can be a critical factor in marketing, challenging the notion that 'lighter' always equates to 'better' in a consumer product.
The metal manufacturing process differs significantly from the plastic manufacturing process. While plastic production often relies on petrochemicals derived from fossil fuels, metal manufacturing has a greater potential for utilizing alternative resources, particularly scrap materials. Innovative technologies like electric arc melting can be used to reprocess scrap steel, emphasizing a circular economy approach in the material utilization for metal cards.
Finally, the inherent structural stability and durability of metal provide a solid foundation for the integration of more sophisticated functionalities. Metal cards can more readily accommodate advanced features like embedded electronics or specialized sensors compared to traditional plastic cards. This is a potential avenue for future developments in smart payment solutions and further enhances the potential advantages of metal as a card material.
American Express Platinum Card's Metal Redesign A Detailed Analysis of Weight, Durability, and Manufacturing Process - Durability Comparison Against Previous Generation Cards 2020 2024
The 2024 American Express Platinum Card demonstrates improved durability compared to its 2020 predecessor. Testing reveals a 40% increase in its resistance to bending, suggesting a significant step forward in material science and manufacturing processes. This advancement, alongside a slight weight reduction, points towards a refined approach to balancing durability and a lighter design. American Express's emphasis on durability in the 2024 model aligns with broader trends seen within the luxury credit card market. It seems the focus is shifting towards cards that are not just aesthetically pleasing but also built to last, suggesting a more refined consumer expectation for these premium products. It remains to be seen how these enhancements will affect consumers' long-term perception and overall satisfaction with the card.
The 2024 American Express Platinum Card demonstrates a significant 40% improvement in bend resistance compared to its 2020 predecessor. This substantial leap highlights advancements in the card's design and engineering, prioritizing durability alongside its aesthetic appeal. It seems that the designers have successfully managed to achieve a robust structure while keeping the weight down.
This remarkable increase in bend resistance suggests that specific design alterations, like tweaking the thickness or refining the edge profiles, can significantly affect a product's structural integrity. This understanding highlights the importance of precision in geometry for achieving desired performance levels.
The rigorous testing methods employed during the card's development probably involved advanced tools such as finite element analysis (FEA). This type of analysis helps simulate stress distribution and pinpoint potential weak points within the design, enabling engineers to fine-tune the design for optimal performance in real-world scenarios. It allows them to build a stronger card without making it too heavy.
Interestingly, simultaneously reducing weight and increasing bend resistance challenges the conventional notion that lighter materials inevitably result in lower durability. This card's design suggests that innovations in material science can lead to solutions that defy traditional material behavior expectations.
The integration of more advanced materials in the 2024 card likely involves the use of high-performance alloys. Ongoing research and experimentation with metal compositions could potentially result in even greater durability without a significant increase in weight for future versions.
Environmental factors, such as temperature changes, can greatly influence the card's performance. Understanding the impact of different climate conditions on stainless steel's properties during regular use provides avenues for optimization and building a card suitable for all types of weather and user behavior.
The integration of contactless payment technology into the 2024 model seems to emphasize improving the card's ability to maintain connectivity and deliver a good performance in different electromagnetic environments. Understanding how these metal cards interact with RF signals, compared to their plastic counterparts, could lead to advancements that result in greater transaction reliability.
The card's manufacturing process and energy requirements not only impact the initial production costs but also the card's long-term durability. The trend towards the use of materials with enhanced strength-to-weight ratios suggests an increasing focus on extending the useful life of metal cards.
The choice of alloying elements within the stainless steel influences not just the card's weight and durability but also its resilience to environmental stress. The inclusion of elements like nickel and molybdenum highlights a meticulous selection process aimed at maximizing the card's performance in a wide range of usage scenarios.
There's a growing trend of seamlessly integrating advanced technology into card design. This might lead to future versions of the card embedding sophisticated electronic components, significantly enhancing their functionality. This path could eventually result in cards that are not only durable but also "smart" when it comes to their payment capabilities.
More Posts from getmtp.com: