Why Aerospace-Grade Aluminum Carry-On Luggage Weighs Less Than Traditional Hard-Shell Options
Why Aerospace-Grade Aluminum Carry-On Luggage Weighs Less Than Traditional Hard-Shell Options - Aluminum Magnesium Alloy Construction Reduces Shell Weight by 30 Percent
The incorporation of aluminum magnesium alloys in luggage construction marks a notable shift towards lighter and more durable travel companions. By combining aluminum and magnesium, manufacturers can reduce the weight of the luggage shell by a substantial 30 percent compared to traditional hard-shell options. This weight reduction is achieved without compromising the shell's structural integrity, a testament to the synergistic nature of these metals.
Furthermore, the addition of manganese to the alloy enhances its properties. This element acts as a stabilizer, inhibiting the recrystallization process that can weaken materials under stress. The result is a stronger, more resilient shell capable of withstanding the rigors of travel.
Interestingly, this trend of utilizing magnesium alloys to minimize weight is mirrored from the aerospace sector. This industry has actively embraced magnesium alloys for their advantageous strength-to-weight ratio, illustrating the potential for these materials to significantly improve luggage performance. Beyond reducing weight, the use of aluminum magnesium alloys also promises increased resistance to wear and tear and potential corrosion, extending the lifespan of the luggage.
Utilizing aluminum magnesium alloys, often classified as 5000 series, in luggage construction results in a remarkable 30% reduction in shell weight compared to conventional hard-shell materials. This weight reduction is achieved by leveraging the inherent properties of these alloys, specifically their lower density compared to other metals commonly employed in luggage production.
The use of these alloys isn't a mere material swap, but a design choice that allows engineers to fine-tune the alloy's microstructure. They are able to manipulate the alloy's composition to optimize it for strength-to-weight ratios and corrosion resistance, both crucial in the demanding environment of air travel. This microstructural optimization, achievable with aluminum magnesium alloys and not easily replicated with purely aluminum or magnesium, enables designers to achieve a level of lightweight structural integrity that surpasses what was previously possible.
Furthermore, the fabrication processes involved in creating these alloys, including techniques like extrusion and thermomechanical treatments, play a significant role in achieving the desired properties. These processes involve precise temperature control and mechanical manipulation of the alloy's grain structure, contributing to its enhanced impact and fatigue resistance, despite the reduced weight.
It's interesting to note that the presence of magnesium in aluminum significantly bolsters aluminum's natural corrosion resistance. This is particularly noteworthy in aviation, where exposure to diverse environments is a constant factor. The corrosion resistance of aluminum magnesium alloys, along with their high strength and tailored microstructure, positions them as a compelling alternative for the future of luggage design, potentially influencing other applications within transportation as well.
Why Aerospace-Grade Aluminum Carry-On Luggage Weighs Less Than Traditional Hard-Shell Options - Material Thickness at 2mm Versus Traditional 4mm Hard Shell Design
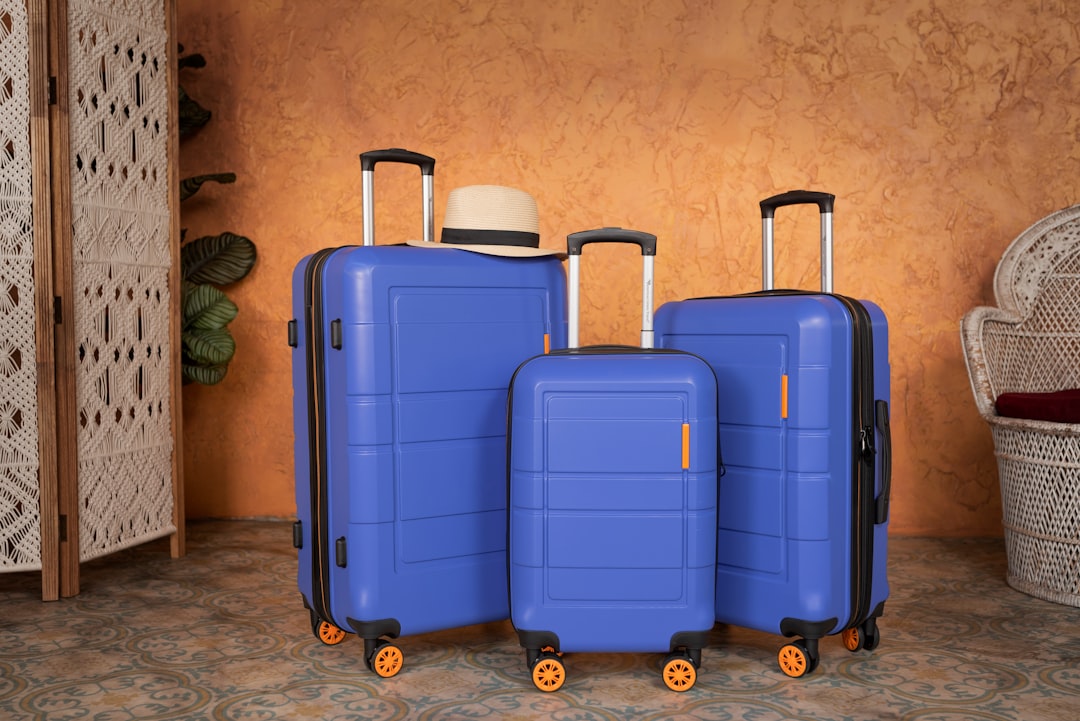
The transition from traditional 4mm hard-shell luggage to a design featuring 2mm aerospace-grade aluminum highlights a significant shift in material thickness and its impact on weight. This thinner aluminum shell, while seemingly less substantial, contributes substantially to the overall lighter weight of these carry-on options. It challenges the conventional notion that thicker materials are inherently more durable, demonstrating that strength and resilience can be achieved with a thinner profile.
Traditionally, hard-shell luggage often utilizes materials like polycarbonate or ABS, prioritizing impact resistance and flexibility. However, this comes at the cost of a heavier overall product, primarily due to the necessity of thicker construction to achieve those desired properties. This illustrates a trade-off between durability and weight in traditional designs.
The move toward 2mm aerospace-grade aluminum represents an innovative approach. It showcases how modern material science allows for lighter designs without compromising on necessary durability. This approach forces a re-evaluation of the connection between luggage thickness and its ability to protect contents. Travelers might now realize that significant weight savings are possible without sacrificing the integrity of their luggage, potentially leading them to reconsider what is essential in a quality carry-on.
The use of 2mm thick aerospace-grade aluminum in luggage construction is a significant departure from the traditional 4mm thick hard shell designs commonly found in polycarbonate or ABS luggage. While seemingly thinner, the 2mm aluminum shell, particularly when constructed from aluminum magnesium alloys, can offer comparable, and in some cases, superior structural performance. This is due to the enhanced yield strength and toughness inherent in these alloys, allowing them to distribute stress effectively during impacts. It's fascinating to observe that the 2mm design often exhibits improved energy absorption during impacts, potentially mitigating the kind of localized damage seen in thicker but potentially more brittle shells. This is a result of the alloy's microstructural properties, which allow for a broader distribution of stress.
Beyond the weight savings, the thinner 2mm shell enables more design flexibility. Engineers can explore complex shapes and ergonomic contours that are difficult to achieve with thicker materials, creating luggage that aligns better with modern aesthetics and user comfort, all without compromising on the shell's structural integrity. Further, the reduction in overall shell thickness can also create a more streamlined luggage profile, potentially improving aerodynamics, a factor that could contribute to improved fuel efficiency, especially in aircraft cargo holds.
Moreover, the shift towards thinner shells opens the door to advanced manufacturing techniques like hydroforming. These processes offer greater design control and can realize intricate shapes that are less feasible with traditional mold-based fabrication methods, making them a valuable asset to modern luggage design. Interestingly, the 2mm shell can be engineered for exceptional dent and deformation resistance due to the aluminum alloy's grain structure, which distributes stresses more evenly than many thicker shells. This capability directly challenges the commonly held assumption that thicker materials are automatically more durable.
The materials utilized in these thinner shells also benefit from specific thermomechanical treatments. These treatments enhance the phase stability of the alloy, ensuring that the shell retains its structural integrity under varying temperature conditions, a crucial consideration during the rigors of airline transport. Further, it’s important to emphasize that material quality is paramount. A 2mm shell crafted from a high-quality aluminum alloy can surpass lower-grade 4mm alternatives in demanding real-world testing scenarios. This highlights the point that material quality, and not just thickness, is essential in achieving optimal performance. Furthermore, innovations in surface coatings for these thinner shells offer increased scratch resistance, enhancing the visual longevity of the luggage, a concern often raised with traditional thicker shells that are more prone to visible wear and tear.
In conclusion, the shift towards 2mm aerospace-grade aluminum in luggage represents a notable alteration in design thinking. The focus is on engineering a product where weight reduction and enhanced performance take priority over simply relying on the thickness of the material. This philosophy leads to innovative luggage designs that not only compete with but arguably surpass the capabilities of traditional hard-shell luggage, thus challenging conventional wisdom in this field.
Why Aerospace-Grade Aluminum Carry-On Luggage Weighs Less Than Traditional Hard-Shell Options - Integrated Frame Design Eliminates Need for Additional Support Structure
The integrated frame design used in aerospace-grade aluminum luggage represents a departure from traditional luggage construction. By integrating the frame directly into the shell, it removes the need for separate, heavier support structures that are often found in traditional designs. This integrated approach allows for a more efficient distribution of weight and stress, leading to a stronger and lighter product. This is a direct result of learning and design practices from the aerospace sector, where maximizing structural efficiency while minimizing weight is a primary design goal.
While traditional hard-shell luggage often relies on thicker materials to achieve rigidity, this integrated frame design, coupled with the use of high-strength aluminum alloys, enables designers to use thinner shells without compromising on performance or durability. This innovative approach challenges the conventional idea that structural strength necessitates heavier materials. This new design philosophy has the potential to transform how luggage is constructed and optimized for various travel situations. Ultimately, this shift reflects a move towards luggage that’s not just lighter, but potentially more structurally efficient and optimized for today's travelers. It highlights the ever-evolving world of luggage design, where innovation and materials science are leading to significant improvements in functionality and aesthetics.
Integrated frame design in luggage draws inspiration from aerospace engineering, where minimizing the need for extra support structures is crucial. By strategically integrating the frame into the luggage's shell, manufacturers can significantly reduce overall weight without compromising durability. This approach challenges the traditional assumption that robust structures require bulky, independent supports.
One benefit of this integrated approach is a more streamlined design. The absence of separate, potentially bulky, support structures not only contributes to a cleaner aesthetic but also maximizes the interior space of the luggage. This space optimization allows travelers to pack more efficiently and potentially carry a greater volume of items.
Furthermore, the integrated frame design allows for a more efficient distribution of internal stress and force. The ability to distribute loads throughout the frame minimizes localized stress points that can lead to structural failure. The use of specialized CAD (computer-aided design) tools allows engineers to perform rigorous simulations of integrated frame designs, enabling them to anticipate and mitigate potential weaknesses before a physical prototype is even built. This analytical approach helps ensure the luggage’s structural integrity under various stress scenarios and conditions encountered during travel.
Interestingly, this approach may even contribute to enhanced aerodynamics during travel. The smoother exterior profile, resulting from the absence of protrusions associated with separate support structures, could potentially reduce drag, which might lead to, albeit potentially small, fuel efficiency improvements when the luggage is in aircraft cargo holds.
This integrated design principle, rooted in the fundamental physics of force distribution, demonstrates that a continuous support structure can better manage stresses than a design with numerous separate joints or supports. Each connection point in a traditional framework represents a potential area of weakness, a concern minimized in the integrated frame approach.
It's also worth noting that this integrated approach may simplify the manufacturing process. The reduction in the number of separate components reduces the risk of defects during assembly, potentially improving the quality control and reliability of the finished product. The fewer components and smoother production process can also potentially reduce manufacturing waste, although this alone shouldn't be a primary design metric.
Looking beyond luggage, the concept of integrated frames reflects a broader trend in engineering across sectors like automotive and aerospace, where weight reduction without sacrificing structural integrity is paramount. This cross-industry application of design principles accelerates innovation in the luggage design space and suggests further opportunities for advancement.
The application of sophisticated computational tools such as finite element analysis (FEA) further underscores the precision and refinement of integrated frame designs. FEA allows engineers to predict and visualize stress concentrations within the structure, leading to more optimized designs capable of withstanding real-world forces and impacts. This advanced analysis provides a level of design assurance that was not possible with older design methods.
This evolution in luggage construction highlights the power of integrated designs, where form and function are carefully considered to achieve an optimally lightweight and durable product. It's an approach that has proven its value in other sectors and shows promise for driving future innovations in the design of travel goods.
Why Aerospace-Grade Aluminum Carry-On Luggage Weighs Less Than Traditional Hard-Shell Options - Heat Treatment Process Creates Stronger Material Without Weight Penalty
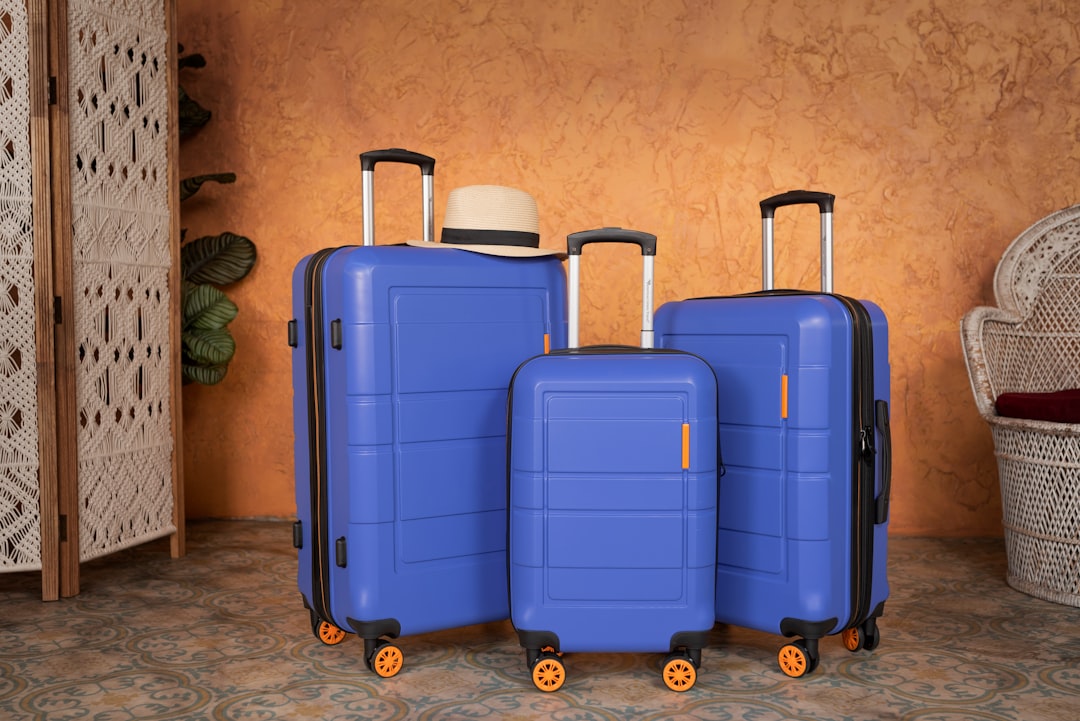
Heat treating aluminum alloys is a key innovation in materials science, allowing for substantial strength improvements without adding weight. Processes like precipitation hardening and aging refine the properties of aerospace-grade aluminum, pushing its performance higher while keeping it light. This leads to materials with enhanced hardness and improved resilience to repetitive stress, making them well-suited for demanding situations like those faced in the aviation industry. The fact that these treatments can produce such significant strength increases compared to older materials is quite remarkable, challenging the long-held belief that heavier materials are always stronger. By incorporating these advanced alloys into carry-on luggage, manufacturers can create luggage that is lighter, but also stronger and more resistant to damage than traditional hard-shell luggage options.
Aluminum magnesium alloys, the backbone of many modern lightweight luggage designs, undergo a series of heat treatments to maximize their performance. These thermal processes, akin to carefully orchestrated cooking methods, manipulate the internal structure of the alloy, resulting in significant enhancements to its mechanical properties.
One key aspect involves rapid cooling, known as quenching. This step helps create a supersaturated solid solution within the alloy, dramatically boosting its tensile strength. In simpler terms, this means the luggage can bear heavier loads without deforming. This is somewhat surprising, as rapid cooling isn't typically associated with improving strength in many materials.
The heat treatments also refine the alloy's internal structure, refining grain boundaries and making the material more uniform. This structural refinement plays a key role in improving impact resistance, a critical aspect for luggage subjected to the rigors of travel and potential bumps.
Furthermore, a process called age hardening allows the alloy to continue strengthening over time. This is a fascinating aspect of the material's behavior—it gets tougher with use, naturally counteracting wear and fatigue.
While seemingly counterintuitive, heat-treated aluminum magnesium alloys can achieve a strength-to-weight ratio comparable to, or even exceeding, much thicker traditional luggage materials. This exemplifies that strength isn't solely determined by thickness, but by carefully controlled internal structure.
Heat treatment positively affects more than just mechanical performance. It also bolsters the corrosion resistance of these alloys. This is advantageous, as luggage is exposed to varying humidities, like those encountered within airplane cargo holds.
Further, these heat treatments enable the luggage to withstand higher temperatures without sacrificing strength. This is particularly important in environments like aircraft overhead bins, where temperature fluctuations are common.
There is a fascinating interplay between material thickness and brittleness that can be impacted by heat treatment. Thin, improperly treated materials can become brittle under stress, but with the right heat treatment, the desired level of ductility can be maintained, reducing the likelihood of cracking during impacts.
While the initial cost of these heat-treated alloys might be higher than traditional materials, their extended lifespan and reduced failure rates can result in long-term cost efficiency. This is due to potentially fewer repairs and replacements, contributing to a more sustainable product.
The development of new heat treatment techniques, such as refining the material's grain structure, is pushing the boundaries of luggage design. Manufacturers now have the ability to precisely tailor the material's properties to the specific demands of luggage, achieving a new level of performance and setting new standards for a balance between durability and weight reduction in travel goods. It’s a promising avenue that shows how materials science can lead to innovations in everyday products.
Why Aerospace-Grade Aluminum Carry-On Luggage Weighs Less Than Traditional Hard-Shell Options - Single Piece Construction Removes Heavy Connection Points
The use of a single piece of aerospace-grade aluminum in luggage construction eliminates the need for multiple pieces and their connecting hardware. These connection points, common in traditional hard-shell luggage, contribute significantly to overall weight. By removing them, the single-piece approach leads to a noticeable weight reduction.
This streamlined approach to design isn't just about shedding pounds; it also strengthens the luggage's structural integrity. Because the aluminum is a single piece, stress is distributed more effectively, lessening the chance of weak points that can occur where different parts are joined together. This integrated design philosophy directly draws on practices from the aerospace sector, where strength and minimal weight are essential. The shift towards single-piece construction in luggage signifies how materials science is shaping product design, making luggage lighter without sacrificing the protection and durability travelers need. It's an example of how a seemingly small change in design can lead to real-world benefits.
Single-piece construction, a technique borrowed from the aerospace industry, offers intriguing advantages for luggage design, particularly in terms of weight reduction and structural integrity. It fundamentally alters how luggage is built, moving away from the traditional approach of multiple connected components.
One of the most notable impacts is the elimination of numerous connection points that are common in conventional hard-shell luggage. These connection points, while necessary in some designs, are potential weak points, susceptible to stress fractures or failure over time, particularly under the repeated stress of travel. By integrating the frame directly into the shell as a single unit, we see a significant reduction in potential failure sites, strengthening the luggage structure overall. This is especially noticeable during more stressful travel events like turbulence or rough handling during baggage transfers.
Furthermore, this design approach leads to a more efficient distribution of weight and stress across the entire luggage structure. The seamless integration of the frame eliminates localized stress hotspots that can develop over time in designs with multiple components and joints. This, in turn, allows manufacturers to design luggage that is thinner and therefore lighter without sacrificing overall strength. While it might appear counterintuitive that a thinner shell can be as strong or even stronger than a thicker one, the optimized weight distribution in single-piece constructions plays a critical role in this.
This seamless construction also has a subtle but potentially meaningful impact on aerodynamics. The smooth, unbroken surface of a single-piece shell, devoid of the protrusions often found at connection points, can potentially reduce air resistance. While it's a small factor, this reduction in drag during flights could contribute marginally to fuel efficiency within aircraft cargo holds.
Interestingly, single-piece construction simplifies the manufacturing process. The fewer components involved translate into reduced assembly time and potentially fewer opportunities for errors during production. This simplification can potentially lead to improved quality control and faster production times. It also paves the way for a more streamlined approach to customization. Changes or new designs can be implemented with less concern for component compatibility. It offers a more direct connection between design intent and the final manufactured product.
The integrated frame, achieved through single-piece construction, results in a more continuous load path, which leads to increased load-bearing capacity. In other words, this design is better at managing the stress and strains that occur from carrying and packing heavy items, making it more resistant to potential collapse. It's intriguing how, from a materials science standpoint, a seemingly simple design change has such a far-reaching effect.
Beyond the purely mechanical advantages, single-piece construction also results in improved thermal resistance. The consistent material throughout the design provides greater stability against the large temperature variations often seen in airplane cargo holds or overhead bins. The uniform thermal behavior reduces the likelihood of material degradation or changes in strength across different areas of the luggage.
While it might initially seem like a simple structural shift, single-piece construction represents a more nuanced design approach that requires careful understanding of the interplay between materials, stresses, and production methods. Through techniques such as finite element analysis (FEA), we can better predict and anticipate how these designs will perform in real-world conditions. This type of analysis helps engineers to identify and refine potentially weak areas and improve designs iteratively, leading to a higher degree of confidence in the end product.
The shift towards single-piece construction suggests a potential trend towards a new philosophy in luggage design, one that seeks to optimize both form and function for greater durability and longevity. By minimizing the number of potential failure points and efficiently managing stress throughout the structure, we see the possibility for luggage that not only lasts longer but potentially delivers better performance during the rigors of air travel. It's a fascinating example of how a change in design thinking can lead to substantial improvements in a commonplace product.
Why Aerospace-Grade Aluminum Carry-On Luggage Weighs Less Than Traditional Hard-Shell Options - Ribbed Pattern Engineering Adds Strength While Using Less Material
Ribbed patterns in engineering offer a smart way to make materials stronger while using less of them. This is a valuable approach, especially in areas like aerospace-grade aluminum luggage, where finding the perfect balance of light weight and durability is crucial. By strategically incorporating ribs into the luggage's design, engineers can spread out the force and stress more evenly. This means the luggage shell can be thinner and lighter without losing any strength. It's a challenge to the old way of thinking where thicker material automatically meant better durability. This type of clever engineering highlights a trend in design that focuses on using materials as effectively as possible to get the best results. Ultimately, this method shows how luggage design can be improved significantly, offering a lighter and stronger product for today's travelers.
Ribbed patterns in aerospace-grade aluminum luggage aren't just a decorative element; they play a critical role in enhancing structural integrity while using less material. It's fascinating how these seemingly simple ridges can significantly boost the load-bearing capacity of the luggage shell. The geometry of the ribs allows for a more efficient distribution of stress, effectively spreading out forces applied to the surface. This means the shell can resist deformation under pressure without needing to be excessively thick, challenging the traditional assumption that greater thickness equates to superior strength.
Interestingly, this ribbed design principle translates into a more efficient use of material. By carefully placing the ribs in areas that experience the most stress, manufacturers can reduce the overall amount of aluminum needed to maintain the desired level of strength. This optimization effectively defies conventional expectations about the relationship between material thickness and structural performance, especially for luggage shells. One has to wonder whether we've been overly reliant on thickness in the past, when optimized geometry might be a more effective solution.
The impact management properties of the ribbed design are also noteworthy. These ribs provide a way to manage and distribute impacts, potentially minimizing the risk of localized failures. This is particularly important in luggage that is subjected to the rigors of travel, including the occasional rough handling and unexpected bumps. Compared to flat-surface luggage designs that often exhibit more pronounced weak points, the ribs create a more resilient structure by spreading out forces and reducing the likelihood of damage in a specific area.
Of course, the weight reduction aspect of this design is critical for luggage. It's a fundamental requirement for many travelers and is often a driving factor in purchasing decisions, especially when airlines place limits on the weight of carry-on luggage. The engineered shape of the ribs, requiring less material for a comparable strength level, directly addresses this need for lightweight luggage.
It's also worth acknowledging the role of advanced manufacturing techniques in achieving the precise and intricate ribbed patterns. Technologies like CNC machining allow for incredibly accurate and repeatable production of these patterns, ensuring that the resulting luggage meets the high standards expected for products using aerospace-grade materials. However, one must consider whether the investment in such advanced methods is justified from a sustainability perspective; perhaps less complex methods could produce functional designs.
Moreover, the ribbed design seems to offer enhanced thermal stability. As temperatures fluctuate, especially within an airplane's cargo hold or overhead bins, the ribs can potentially better accommodate the differential expansion and contraction of the aluminum material, reducing the risk of warping or other structural compromises. This is intriguing from a materials science perspective, as it shows how the design can interact with the material properties to improve overall performance. But it also raises questions about whether this is a substantial advantage or simply a byproduct of the design.
In terms of product lifecycle, the ribbed pattern might contribute to a longer life span of the luggage. The improved stress distribution achieved through the ribbed structure could potentially minimize material fatigue, which is a major factor in the degradation and failure of many luggage designs. However, it remains to be seen whether these benefits outweigh the increased manufacturing complexity and cost.
Beyond their mechanical advantages, ribbed patterns offer an aesthetic opportunity, adding a distinct and potentially modern visual element to luggage design. It's interesting how design elements can play multiple roles in product engineering, balancing functionality with aesthetics.
Finally, it's worth considering that the application of ribbed patterns extends beyond just luggage. This design principle is used in other engineering disciplines, such as automotive and aerospace design, demonstrating the versatility and effectiveness of this structural approach across diverse industries. It's compelling evidence of how a single design element can be leveraged across various application spaces and highlight opportunities for broader optimization of materials and structures.
While the benefits of ribbed patterns in aerospace-grade aluminum luggage are intriguing, it's essential to continue research and development in this area to better understand the long-term impacts of this design choice on performance, cost, and sustainability. There is a growing need for a thoughtful and critical assessment of innovations as they emerge and are implemented in everyday products.
More Posts from getmtp.com: